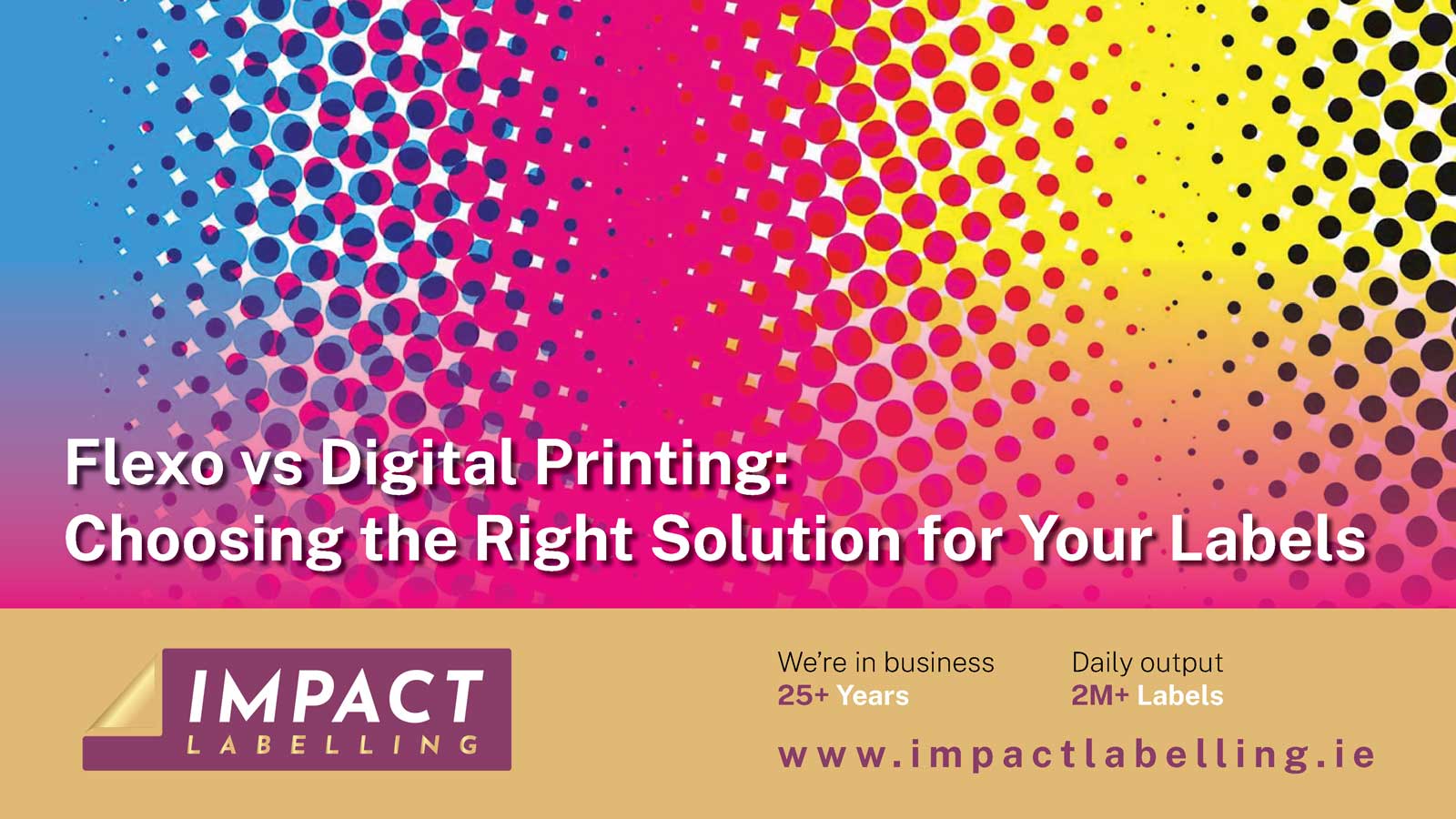
When it comes to label printing, the choice between flexographic (flexo) and digital printing is crucial, affecting both the quality and cost-effectiveness of your project. Each method has distinct advantages and is better suited to different types of jobs. This guide will explore the merits of flexo and digital printing to help you make an informed decision for your labelling needs.
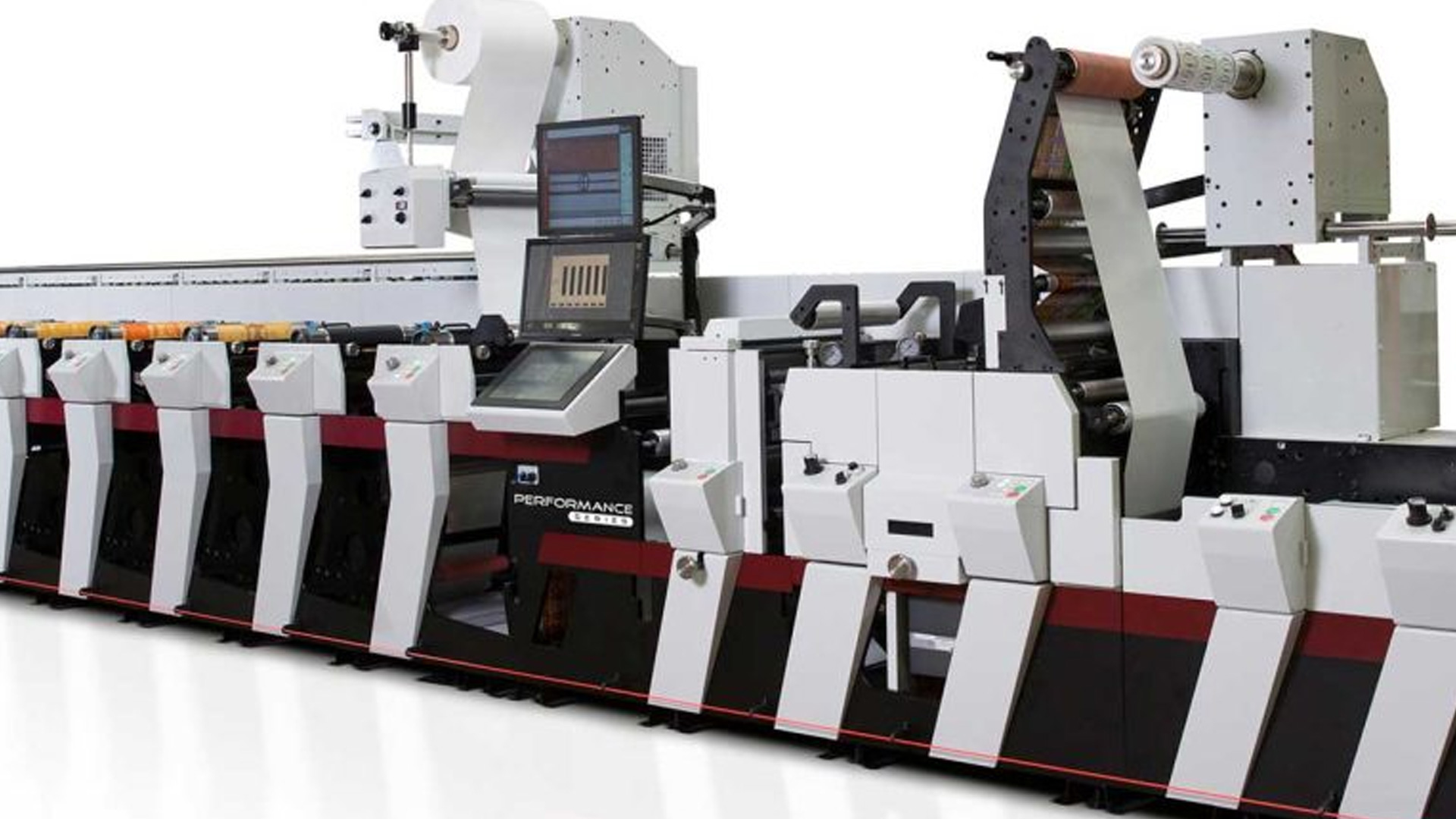
Flexographic Printing: Traditional and Efficient
Advantages of Flexo Printing
- Cost-Effective for Long Runs: Flexo printing shines in high-volume projects. The initial setup costs, including creating printing plates for each colour, are offset by the lower per-unit cost in large runs. This makes it an economical choice for substantial label quantities
- Versatility in Substrates: Flexo can print on a wide range of materials, from paper to plastic, foil, and even metallic films. This flexibility makes it ideal for diverse packaging needs, such as food packaging, beverage labels, and industrial products
- High-Speed Production: Flexo presses operate at high speeds, making them suitable for large orders that need quick turnaround times. The process is efficient, particularly for jobs that don’t require frequent changes in design or colour
- Durability and Quality: Flexo prints are known for their durability, able to withstand harsh conditions like exposure to moisture, chemicals, and varying temperatures. This makes it a preferred choice for labels on items like chemical containers and motor parts
Limitations of Flexo Printing
- Higher Initial Setup Costs: The need for custom plates for each colour makes flexo less suitable for short runs or projects requiring frequent design changes
- Complexity in Colour Matching: While flexo can achieve excellent colour consistency, the process of changing or adjusting colours involves creating new plates, which adds to the complexity and cost

Digital Printing: Modern and Flexible
Advantages of Digital Printing
- Low Setup Costs and Quick Turnaround: Digital printing doesn’t require plates, which eliminates setup costs and significantly reduces the time from design to finished product. This makes it ideal for short runs and projects with tight deadlines
- High-Quality and Detailed Prints: Digital printing excels in producing high-resolution images with intricate details, making it perfect for photo-quality labels and complex designs. The ability to easily manage colour calibrations ensures consistent quality throughout the print run
- Customisation and Variable Data: One of the biggest strengths of digital printing is its ability to handle variable data efficiently. This means you can print labels with unique information, such as personalised names or serial numbers, without additional cost or setup time. This feature was famously used in the Coca-Cola “Share a Coke” campaign
- Environmentally Friendly: Digital printing produces less waste compared to flexo, as it does not require excess materials for setup or changeovers. This makes it a more sustainable option for eco-conscious brands
Limitations of Digital Printing
- Higher Cost for Large Volumes: While cost-effective for small to medium runs, digital printing becomes less economical as the order size increases. The per-unit cost remains relatively constant regardless of the volume, which can be a drawback for large-scale projects
- Limited Substrate Compatibility: Digital printing is less versatile than flexo in terms of the materials it can print on. Certain substrates and finishes might require additional steps, such as lamination, which can increase production time and cost
Making the Right Choice
Choosing between flexo and digital printing depends on several factors, including the size of your print run, the complexity of your design, your budget, and the turnaround time. Here are some guidelines to help you decide:
- Large Volumes with Simple Designs: Opt for flexo printing to benefit from lower per-unit costs and high-speed production
- Small to Medium Runs with Complex Designs: Choose digital printing for its low setup costs, quick turnaround, and high-quality output
- Variable Data or Personalised Labels: Digital printing is the clear choice for projects requiring customisation or variable data printing
- Durability and Versatility Needs: If your labels need to withstand harsh conditions or be printed on unconventional materials, flexo printing might be more suitable.
By considering these factors, you can select the printing method that best aligns with your project’s requirements, ensuring you achieve the desired quality and cost-effectiveness.
For expert guidance on your specific needs, get in touch so we here at Impact Labelling can help you make the best decision for your brand.
When it comes to label printing, the choice between flexographic (flexo) and digital printing is crucial, affecting both the quality and cost-effectiveness of your project. Each method has distinct advantages and is better suited to different types of jobs. This guide will explore the merits of flexo and digital printing to help you make an informed decision for your labelling needs.
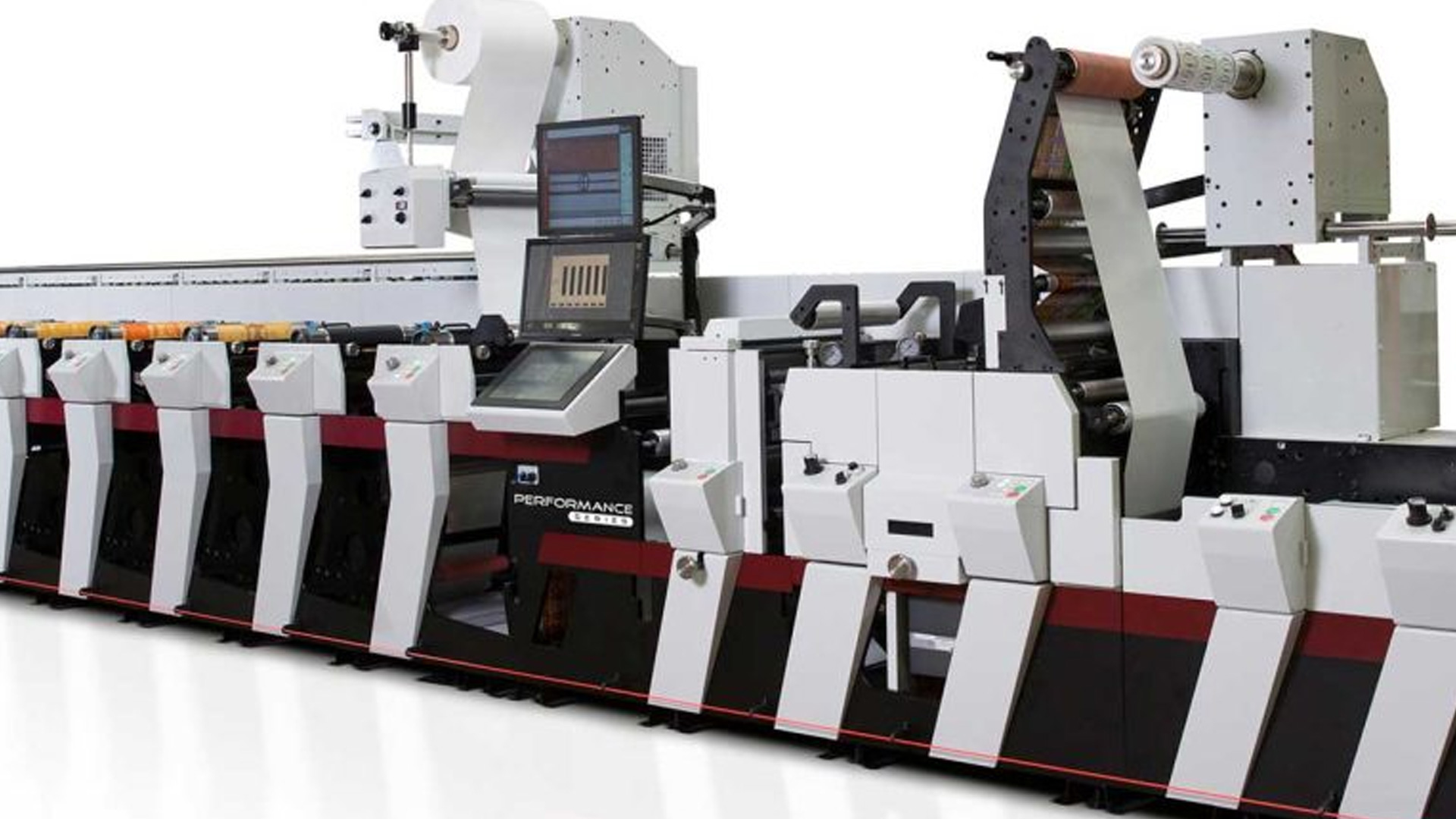
Flexographic Printing: Traditional and Efficient
Advantages of Flexo Printing
- Cost-Effective for Long Runs: Flexo printing shines in high-volume projects. The initial setup costs, including creating printing plates for each colour, are offset by the lower per-unit cost in large runs. This makes it an economical choice for substantial label quantities
- Versatility in Substrates: Flexo can print on a wide range of materials, from paper to plastic, foil, and even metallic films. This flexibility makes it ideal for diverse packaging needs, such as food packaging, beverage labels, and industrial products
- High-Speed Production: Flexo presses operate at high speeds, making them suitable for large orders that need quick turnaround times. The process is efficient, particularly for jobs that don’t require frequent changes in design or colour
- Durability and Quality: Flexo prints are known for their durability, able to withstand harsh conditions like exposure to moisture, chemicals, and varying temperatures. This makes it a preferred choice for labels on items like chemical containers and motor parts
Limitations of Flexo Printing
- Higher Initial Setup Costs: The need for custom plates for each colour makes flexo less suitable for short runs or projects requiring frequent design changes
- Complexity in Colour Matching: While flexo can achieve excellent colour consistency, the process of changing or adjusting colours involves creating new plates, which adds to the complexity and cost

Digital Printing: Modern and Flexible
Advantages of Digital Printing
- Low Setup Costs and Quick Turnaround: Digital printing doesn’t require plates, which eliminates setup costs and significantly reduces the time from design to finished product. This makes it ideal for short runs and projects with tight deadlines
- High-Quality and Detailed Prints: Digital printing excels in producing high-resolution images with intricate details, making it perfect for photo-quality labels and complex designs. The ability to easily manage colour calibrations ensures consistent quality throughout the print run
- Customisation and Variable Data: One of the biggest strengths of digital printing is its ability to handle variable data efficiently. This means you can print labels with unique information, such as personalised names or serial numbers, without additional cost or setup time. This feature was famously used in the Coca-Cola “Share a Coke” campaign
- Environmentally Friendly: Digital printing produces less waste compared to flexo, as it does not require excess materials for setup or changeovers. This makes it a more sustainable option for eco-conscious brands
Limitations of Digital Printing
- Higher Cost for Large Volumes: While cost-effective for small to medium runs, digital printing becomes less economical as the order size increases. The per-unit cost remains relatively constant regardless of the volume, which can be a drawback for large-scale projects
- Limited Substrate Compatibility: Digital printing is less versatile than flexo in terms of the materials it can print on. Certain substrates and finishes might require additional steps, such as lamination, which can increase production time and cost
Making the Right Choice
Choosing between flexo and digital printing depends on several factors, including the size of your print run, the complexity of your design, your budget, and the turnaround time. Here are some guidelines to help you decide:
- Large Volumes with Simple Designs: Opt for flexo printing to benefit from lower per-unit costs and high-speed production
- Small to Medium Runs with Complex Designs: Choose digital printing for its low setup costs, quick turnaround, and high-quality output
- Variable Data or Personalised Labels: Digital printing is the clear choice for projects requiring customisation or variable data printing
- Durability and Versatility Needs: If your labels need to withstand harsh conditions or be printed on unconventional materials, flexo printing might be more suitable.
By considering these factors, you can select the printing method that best aligns with your project’s requirements, ensuring you achieve the desired quality and cost-effectiveness.
For expert guidance on your specific needs, get in touch so we here at Impact Labelling can help you make the best decision for your brand.